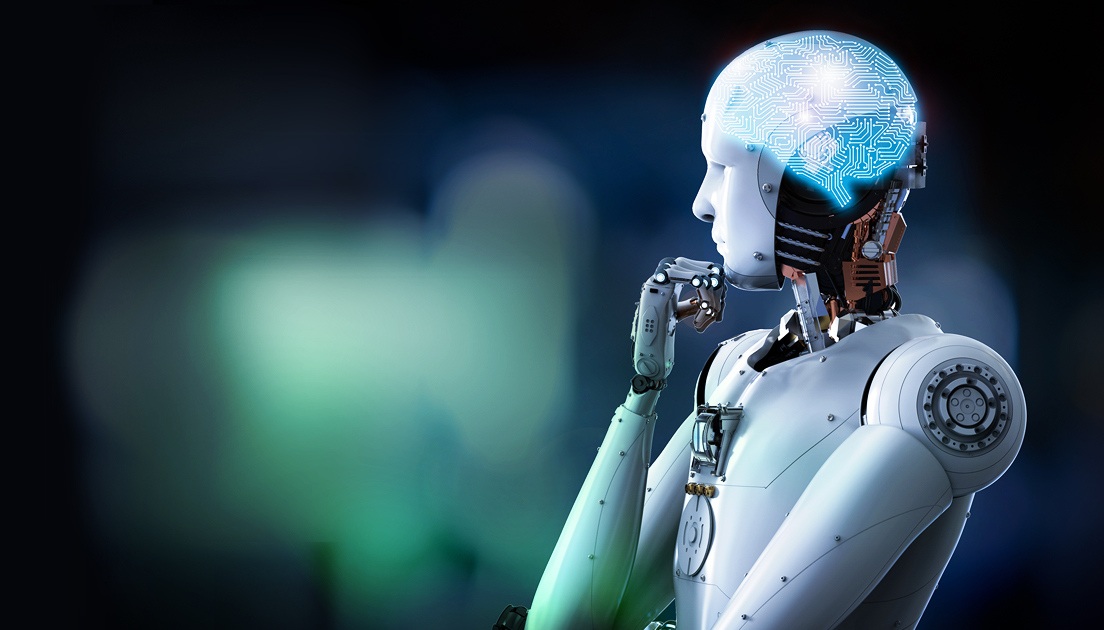

People tend to think that all robots work using artificial intelligence (AI). However, most robots function in accordance with their pre-programmed logical circuits. Robots used in a factory or cleaning robots for households are also programmed to follow their respective logical circuits, and as such they are not “autonomous” in the true sense of the word. In other words, they cannot think for themselves. There are several hurdles to overcome before autonomous robots that are capable of independently accepting and responding to changes in their surrounding environments on a real-time basis can be commercialized.
AI, unlike a logical circuit designed to make robots repeat the same task, enables robots to learn data on their own to handle and respond to a given task in real time. In this sense, it can be said that AI performs a similar role to what the human brain does. In addition, they offer great value for practical use as they perform tasks that are overwhelming for humans in places that humans cannot reach. Currently, robots (Kiva) and unmanned vehicles are garnering a great deal of attention. Most of them are partially autonomous robots whose functions are based mainly on logical structures rather than AI. Some claim that autonomous robots with full AI functionality, like fully self-driving cars, can become a reality within the next 10 years. Then, what technologies is ETRI developing in preparation for the era of autonomous robots?
01
Laying a cornerstone for the development of autonomous robotics
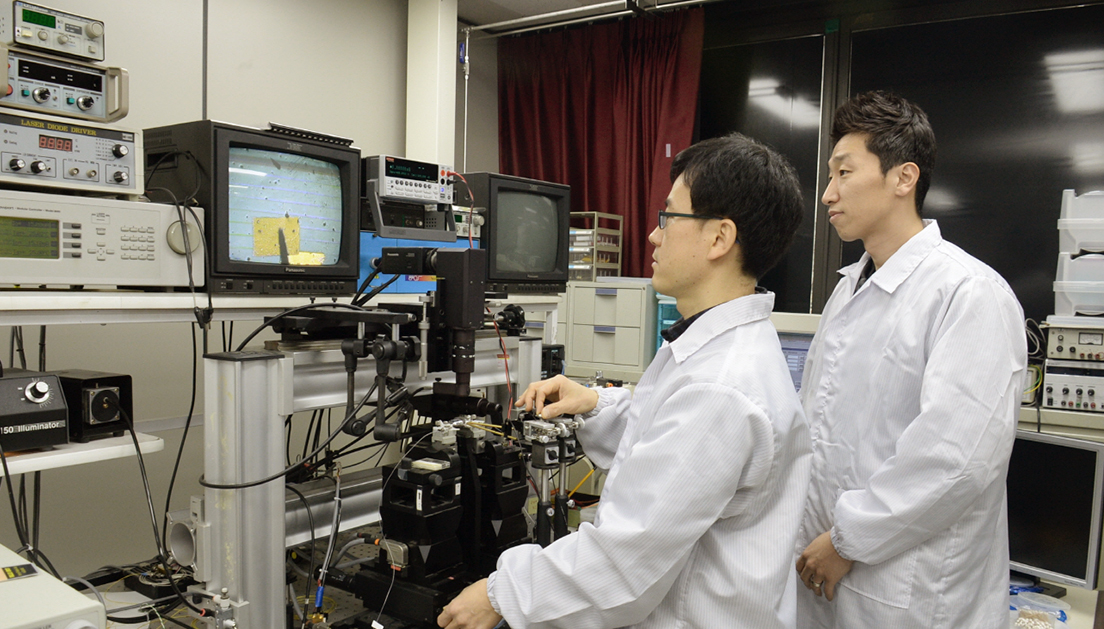
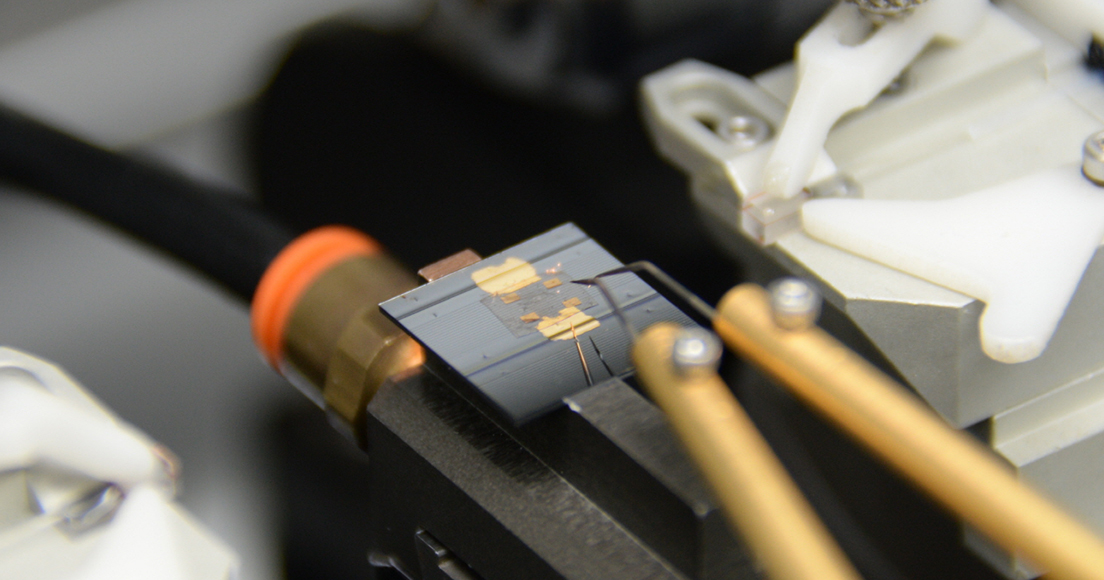
The area for data-saving and the area for calculating coexist in the human brain. However, a computer has separate parts for data-saving and calculating. If the parts for data-saving and calculating can coexist in a computer as in the human brain, it would be able to process and transmit information rapidly while also performing calculation and data-saving simultaneously. This will enable optical computing that mimics the human nervous system in the brain.
To date, researchers at ETRI have been focusing on developing computer chips that resemble the human brain. This is because our brain has the perfect functionality for information delivery. The research team worked hard to control hysteretic behaviors of optical switching devices caused by electrical or optical stimulation in order to emulate the advantages of the human brain structure as they are. As a result, ETRI successfully developed an 'optical synapse-mimic device' that artificially reproduces the synapses of neurons. This laid a foundation for the development of a nerve-mimic optical computing technology that will allow simultaneous memorizing and thinking (calculation) like the human brain does.
The optical memory device developed by ETRI researchers is about 20㎛ x 20㎜. Research is underway to develop devices about several hundred nanometer-level and to realize high integration in the form of chips. Optical synapse-mimic devices overcome the limitations of their electrical synapse-mimic counterparts, as they do not experience any interference between channels and offer low power consumption. In addition, they can use various wavelengths of light, which supports simultaneous computations.
This new device developed by ETRI researchers is anticipated to be embedded in a chip to be used in optical communication for information transmission, to enable transmission of information and computing at once.
ETRI reported that, while it usually takes about 0.06 seconds for humans to see and recognize an object, optical computing, when fully developed, can offer much quicker recognition while consuming less power. Therefore, this technology is expected to serve as an epoch-making milestone in technological advancement in the fields of pattern recognition or voice recognition. The research team says their ultimate goal for the future is to develop a chip that can think for itself.
If existing “thinking” robots are, in reality, pre-programmed robots, the future will see robots that can really think for themselves, says ETRI. With this new development, ETRI has laid a cornerstone for the development of autonomous robotics.
02
Opening the door to the wearables market
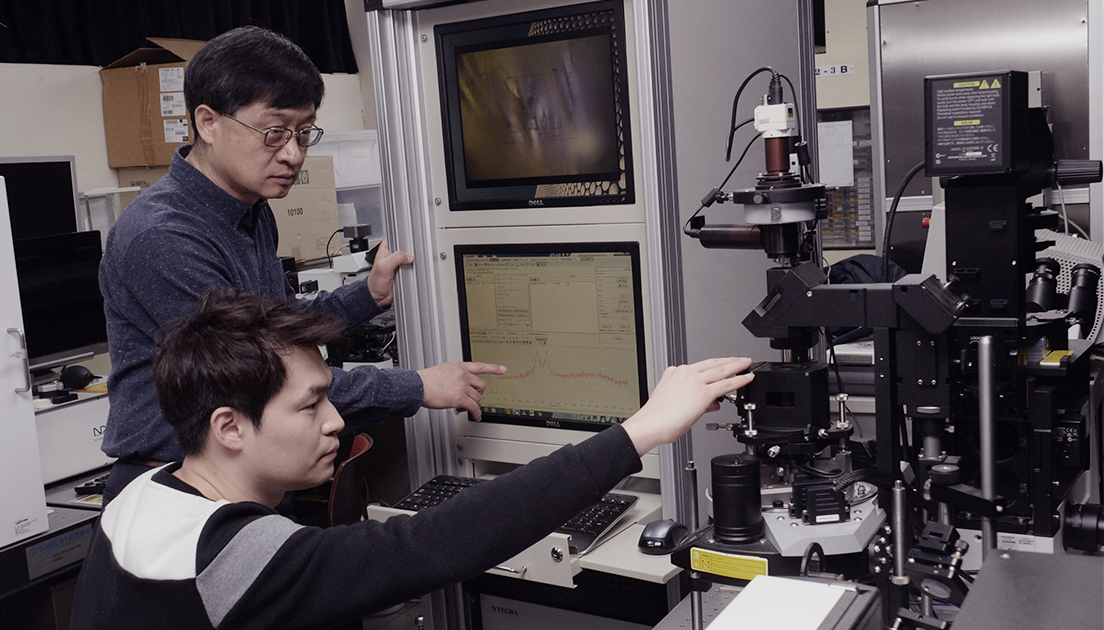
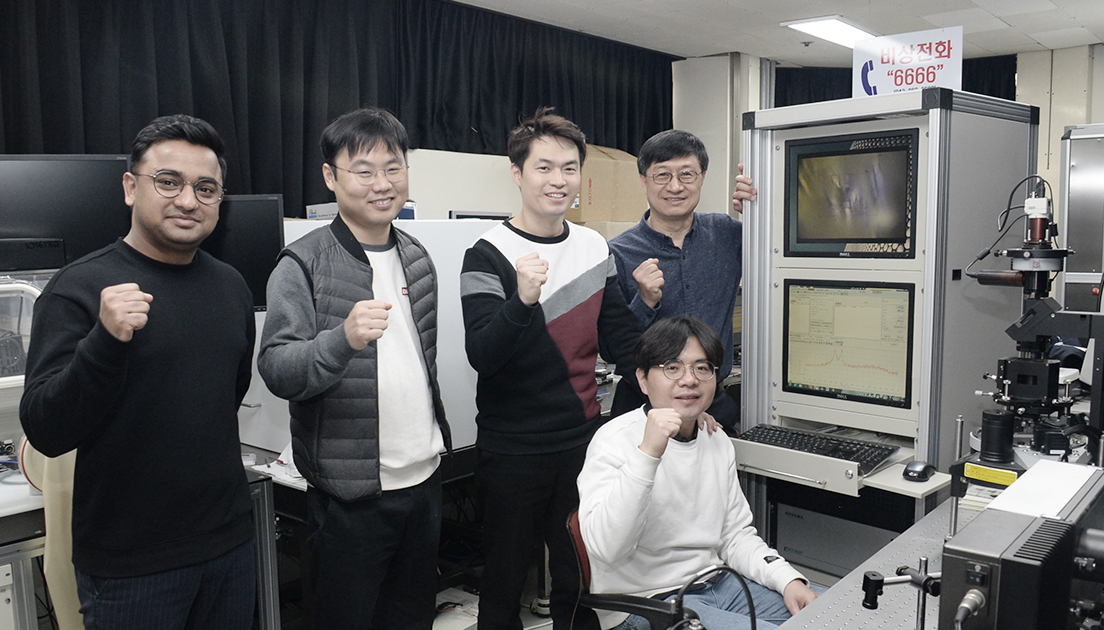
Until now, sensors have mainly used conductive metallic materials that allow good flow of electricity. However, metallic materials have faced challenges in commercialization due to problems in malleability and durability, where the materials would be difficult to bend and would easily break after repeated bending. Setting out to solve this problem, a research team at ETRI endeavored to develop sensors that are thin yet sturdy, and with outstanding chemical stability against sweat and other chemicals.
Such endeavors bore fruit when the ETRI research team successfully developed for the first time a highly conductive fabric-type sensor that can maintain resistance to water even after repeated bending or compression, by coating a cotton textile with a combination of graphene and carbon nanotubes. This fabric-type complex sensor can measure pressure and strain simultaneously, and is produced through a process of submerging and extracting fabric such as cotton in a solution of graphene and carbon nanotubes followed by a drying process. In particular, the sensor’s waterproof characteristics allow washing with no problems, and furthermore it does not require any supplementary functionalities. The team was also successful in building a motion sensor for detecting finger motions by applying the developed sensor to a cotton glove.
The essence of this R&D achievement is that reduced graphene and carbon nanotubes were combined to realize a fabric-type complex sensor capable of pressure and strain sensing. The sensor’s size is approximately 1 cm by 3 cm. However, it can be produced in large dimensions of dozens of centimeters with no limitations in design or size, thus enabling immediate application to fabric without any issues.
Since this technology makes the material itself the sensor, it works identically to conventional fabric coating. Textiles are coated in conductive graphene as they would be coated in dye. As such, the textiles can be cut as desired for use as sensors. Reduced graphene is produced by chemically reducing oxidized graphene, which is produced by oxidizing graphite, the same material used for pencil lead. Since oxidized graphene is an insulator, oxygen (O2) must be removed for the material to attain conductivity.
The graphene-based fabric sensor created through this process can be mass-produced and made to have a variety of characteristics such as superior conductivity, water resistance for better dryness, outstanding flexibility, and large size.
The research team stated that the future plan is to apply the developed sensor to gloves as a wearable item, which will be distributed for use on robotic hands, as well as on prosthetic hands and feet used by disabled people. With this achievement, ETRI has opened wide the doors to the wearable sensors market. The team plans to continue its efforts to commercialize the technology by transferring the tech to prosthetics companies, mattress manufacturers, automobile parts manufacturers, and other related companies.